A new 3D-printed concrete mix made with fossilized diatoms captures 142% more CO₂, promising stronger and greener building materials.
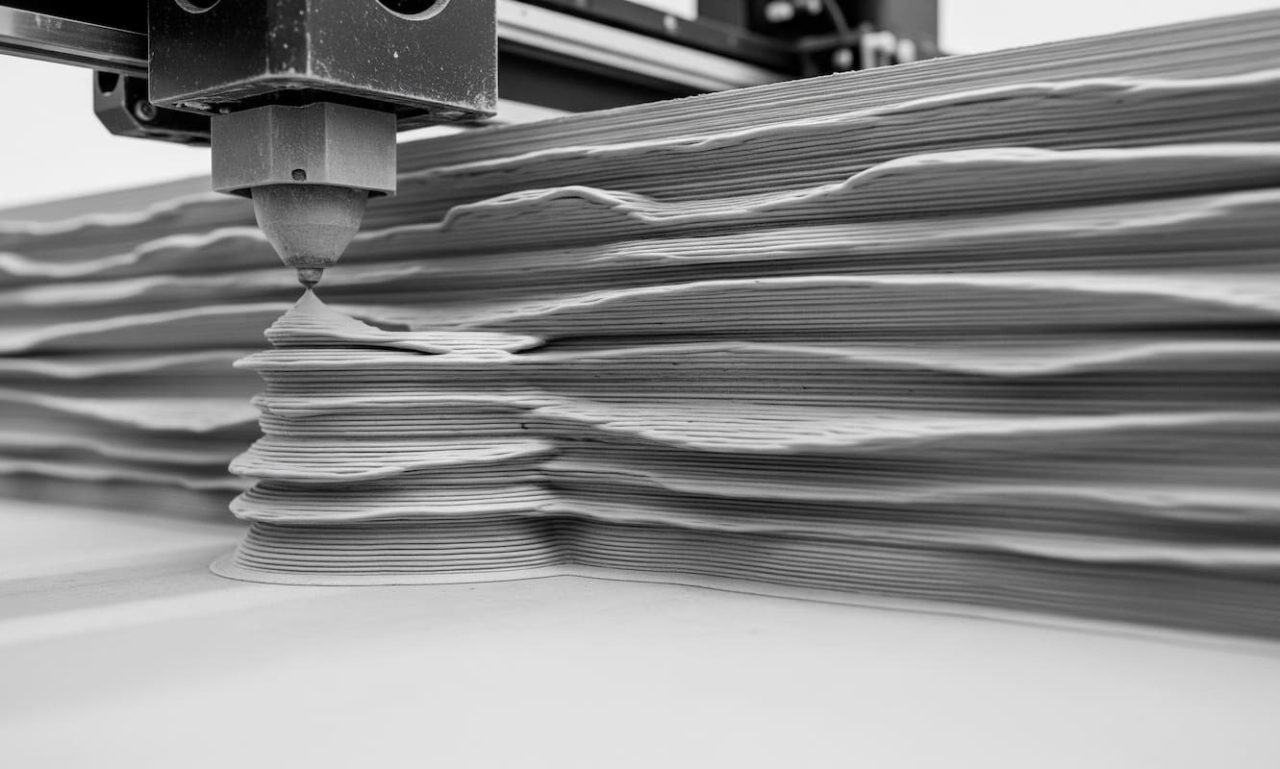
From diatoms to 3D printing, a new path to decarbonization
Concrete, a timeless symbol of human construction, has become a major climate threat. Responsible for around 9% of global greenhouse gas emissions, it remains essential to urban development. This environmental challenge has driven researchers to explore ways to make concrete more sustainable.
An interdisciplinary team at the University of Pennsylvania, bringing together material scientists, architects, and designers, has developed a next-generation sustainable concrete: a 3D-printable mix made with fossilized diatoms that not only reduces cement use but actively captures carbon dioxide from the surrounding air.
Diatomite and 3D printing for carbon capture
The key to this innovative compound is diatomaceous earth, a naturally porous material derived from fossilized shells of siliceous microalgae. Previously used in agriculture and filtration, this powder is now proving ideal for producing low-carbon concrete.
“The sponge-like, porous structure of diatomite not only stabilizes the mix during extrusion through the 3D printer nozzle, it also provides multiple active sites to trap carbon dioxide,” explain the researchers in their study published in Advanced Functional Materials.
The result is a material that uses less cement but achieves compressive strength comparable to traditional concrete, while capturing 142% more CO₂.
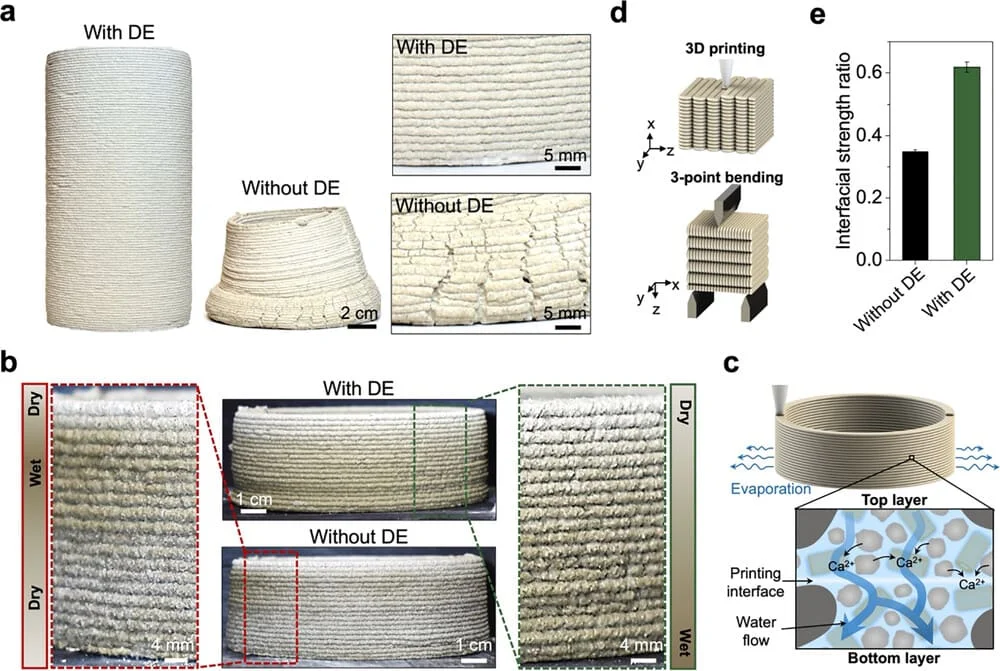
One of the most surprising findings from testing this new material was its strength. Typically, increasing porosity weakens concrete, but in this case, the opposite happened. “The structure became stronger over time,” said Shu Yang, professor and co-author of the study.
By refining the geometry, the team achieved an additional 30% increase in CO₂ conversion, without compromising the mechanical performance required for the construction industry.
A triple benefit: strength, efficiency, and carbon capture
The geometric structure of this sustainable concrete, shaped through 3D printing, plays a crucial role. Researchers adopted triply periodic minimal surfaces (TPMS), complex mathematical forms found in nature, like in bones, corals, and starfish.
“These forms are naturally efficient, maximizing surface area and stiffness while minimizing material use,” said Masoud Akbarzadeh, senior co-author and associate professor of architecture. “In nature, form and function are inseparable, and we wanted to apply that principle to our material design.”
By using principles from mathematics and structural mechanics, the team mapped force distributions within the material to build self-supporting concrete, capable of spanning large overhangs while maintaining optimal porosity for carbon dioxide diffusion.
Scaling up: future applications for buildings and oceans
With lab tests complete, the team is now exploring large-scale applications, including structural panels, façades, and flooring. The material retained 90% of the compressive strength of traditional solid concrete, while gaining an additional 30% CO₂ conversion per unit of cement used.
Beyond construction, the material’s eco-compatibility opens doors for marine applications. Researchers are also testing combinations with Portland cement alternatives, such as magnesium-based binders and alkali-activated systems, to further reduce emissions and enhance sustainability.