Back contact photovoltaics deliver high efficiency and reduced costs, setting the stage for next-gen solar technology integration
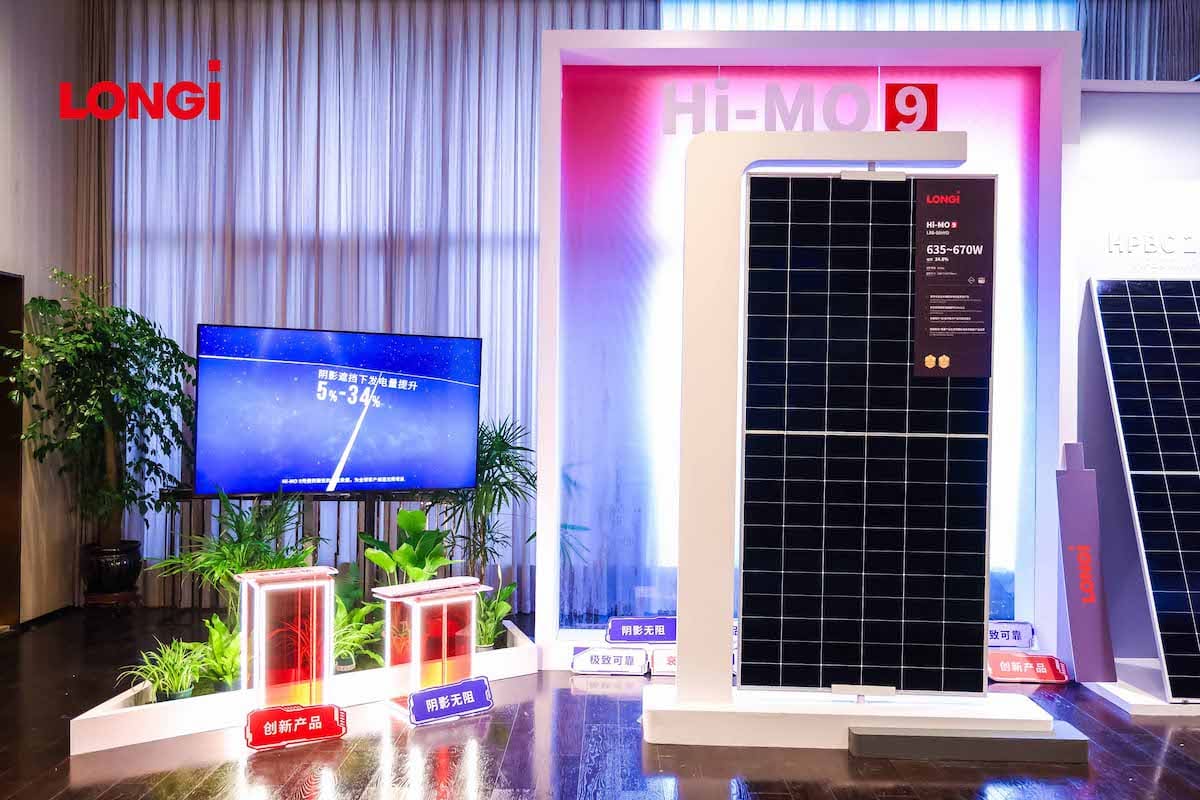
Thanks to lower investment costs and high production efficiency, back contact technology offers unique advantages in the solar industry and strong potential for integration with other solar innovations.
The back contact photovoltaics white paper
Once a niche technology for premium applications, back contact photovoltaics (BC) have now entered the mainstream. They represent the cutting edge of single-junction silicon solar cell evolution.
With mass production now mature and cost-competitive, BC solar modules offer undeniable benefits for manufacturers. These advantages become even more relevant when considering future integration with other core solar technologies. A new white paper presented at Intersolar 2025 by LONGi, Aiko Solar, TÜV Rheinland, the China Electricity Council, and the China General Certification Center outlines these benefits in detail.
The document describes back contact photovoltaics as a foundational platform that can usher in a new solar era, thanks to ongoing research and key breakthroughs that have significantly improved both efficiency and competitiveness.
How back contact photovoltaics work
Back contact (BC) solar cell technology places all positive and negative electrodes on the rear side of the cell using a full rear-side interconnection technique.
This design eliminates the traditional front-side metal busbars, which cause shading, and maximizes the light-absorbing surface area. As a result, it overcomes the efficiency limitations of conventional crystalline silicon solar cells.
Specifically, removing the front metal grid allows more photons to reach the silicon absorber layer. Photon utilization rates are estimated to reach up to 97.3%, leading to higher short-circuit current density (Jsc) and ultimately greater energy conversion efficiency. The latest world record for BC solar cell efficiency stands at 27.81%.
Additionally, this rear-contact architecture eliminates parasitic absorption caused by front-side doping. Full-area passivation with Al₂O₃/SiNx further reduces surface recombination velocity, enhancing the cell’s spectral response.
Field data show that BC modules can generate up to 11% more energy over their lifetime than TOPCon modules. Under partial shading, BC solar panels have demonstrated an energy gain of up to 33%.
A true technology platform
What truly sets back contact photovoltaics apart is their role as a structured electrode platform capable of hybridizing with other mainstream technologies. In simple terms, BC cells can be seamlessly integrated with advanced solutions like heterojunction (HJT), tunnel oxide passivated contact (TOPCon), and even future tandem perovskite architectures.
Two key architectures are currently gaining traction, one in the pilot phase and the other already in commercial production: heterojunction back contact (HBC) and tunneling back contact (TBC) solar technologies.
- HBC solar cells combine the back contact (BC) design with a hydrogenated amorphous silicon (a-Si:H) layer, a defining feature of heterojunction (HJT) cells.
- TBC solar cells pair the back contact structure with a passivated contact formed by a thin silicon dioxide (SiO₂) layer, creating a tunneling contact typical of TOPCon cell technology.
Convergence Technology | Lab Efficiency | Mass Production Module Efficiency | Industrialization Status |
---|---|---|---|
HJT (heterojunction) with hydrogenated amorphous silicon layer + back contact (BC) | 27.81% | / | Pilot line |
TOPCon (tunnel oxide passivated contact) with multicrystalline silicon + BC metallization | ≥27.1% | 24.4% | 2025 >100 GW capacity planned |
Industrial-scale production
Once seen as complex and costly, back contact solar manufacturing has now reached full industrial maturity. The technology marks a major milestone in solar energy production.
In recent years, single-line production capacity has increased more than fivefold. With the rapid development of laser patterning and ongoing improvements in wet processing, the number of steps in BC solar cell manufacturing has been reduced from over 20 to just 12.
This has led to a more than 60% reduction in overall back contact production costs.
(See current BC solar module prices here.)
Another important point: reliability tests consistently show that BC modules outperform TOPCon modules in long-term performance. Below are the test results conducted by TÜV:
Test | Test Standard | BC Module Performance | BC vs TOPCon Performance | Advantage Margin |
---|---|---|---|---|
TC200 (-40°C ↔ +85°C), 200 cycles | IEC 61215 | Degradation 0.53% | Degradation 0.63% | +15.8% |
DH1000 (85°C/85%RH), 1,000 hours | IEC 61215 | Degradation 1.21% | Degradation 1.31% | +7.6% |
PID 96h (85°C/85%RH), 96 hours | IEC 62804 | Degradation 0.92% | Degradation 1.07% | +14% |
LID (Light-Induced Degradation), 60kWh | IEC 61215-2 | Degradation 0.04% | Degradation 0.51% | +90% |
Sequential Test (UV+DML+HF+TC) | / | Degradation 1.02% | Degradation 1.14% | +10.5% |
Ultimate load wind tunnel test (limit wind velocity test) | Wind tunnel test passed at 64.4 m/s (equivalent to scale 18 super typhoon) | / | / | / |
NMOT (Nominal Module Operating Temperature) | IEC 61853-1 | 41.1°C | 41.6°C | 0.5°C |
Hot spot | IEC 61215-2:2021 MQT 09 (hot spot test) | Avg. 138.1°C | Avg. 184.6°C | 46.5°C lower |