A common bacterium transforms plastic waste into the active ingredient of paracetamol, the basis of many painkillers.
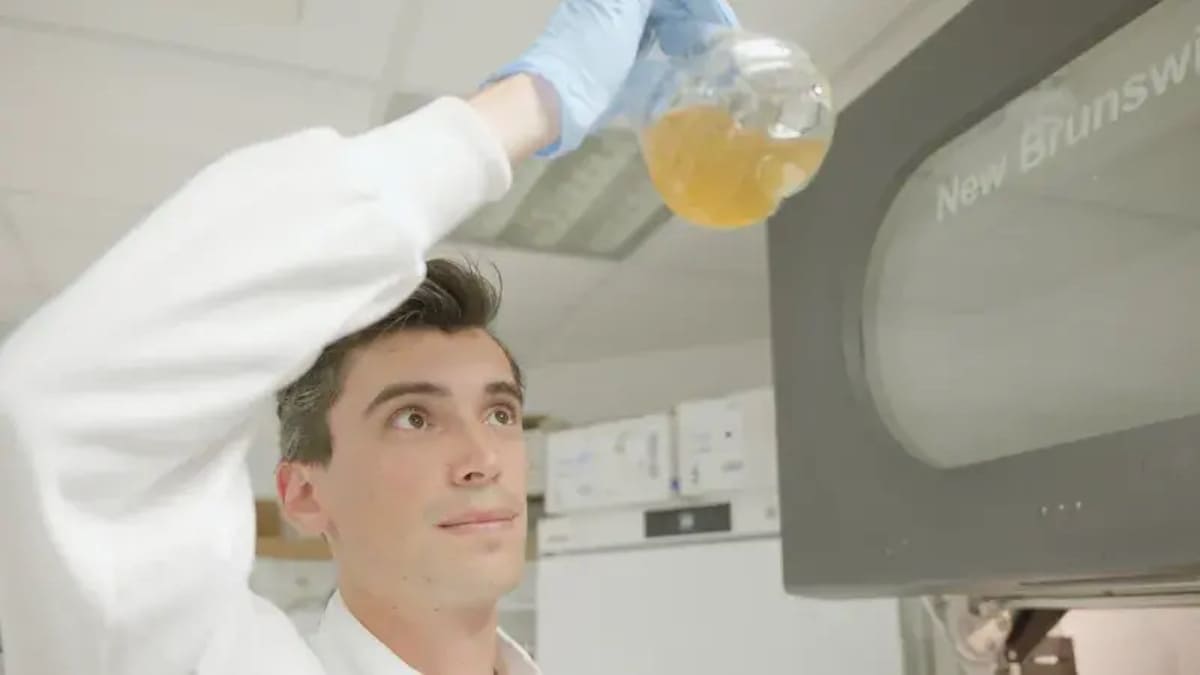
Plastic waste turned into paracetamol: engineered bacteria change the game
One of the world’s most widely used painkillers, paracetamol, could soon be made from plastic waste. A breakthrough by the University of Edinburgh has introduced a zero-carbon emission process that might compete with traditional pharmaceutical production. The secret? A common bacterium. But first, let’s look at how paracetamol is usually made.
How paracetamol is traditionally produced
Paracetamol is typically manufactured in pharmaceutical plants, where many of the base chemicals come from petroleum products, all of which are fossil fuels. These factories also demand a significant amount of energy to drive synthesis, heating, and cooling processes, energy that mainly comes from burning coal, natural gas, and oil. As a result, paracetamol production is linked to greenhouse gas emissions and contributes to climate change.
PET and the global plastic pollution crisis
Researchers at the University of Edinburgh believe the solution may lie in recycling polyethylene terephthalate, or PET, one of the most widely used plastics. PET is commonly found in beverage bottles and is a major source of plastic waste, much of which ends up in landfills or pollutes the oceans, forming massive plastic islands.
Despite being lightweight and durable, PET is responsible for over 350 million tons of plastic waste generated each year, causing significant environmental harm. Although PET is technically recyclable, current recycling methods fail to effectively remove it from the environment.
A harmless bacterium with powerful capabilities
Here’s where the innovation begins. Scientists from the Wallace Lab at the University of Edinburgh genetically reprogrammed the widely known Escherichia coli bacterium to convert terephthalic acid, a molecule derived from PET, into the active ingredient of paracetamol.
Using a fermentation process similar to beer brewing, the team accelerated the conversion of PET waste into paracetamol in less than 24 hours. The method was carried out at room temperature and generated zero carbon emissions, proving that sustainable drug production is possible.
While commercial-scale production is still in development, results showed that around 90% of the product resulting from the interaction between terephthalic acid and genetically engineered E. coli was paracetamol.
“This work demonstrates that PET plastic is not just waste or material destined to become more plastic, it can be transformed by microorganisms into valuable new products,” said Professor Stephen Wallace, who led the study.
The Edinburgh breakthrough
According to experts at the University of Edinburgh, a global leader in biological engineering, this innovation shows how traditional chemistry can work hand in hand with synthetic biology to build living microbial factories capable of producing sustainable chemicals. It offers a path to reducing waste, cutting greenhouse gas emissions, and decreasing reliance on fossil fuels.
The research, published in Nature Chemistry, is now drawing interest from a major biopharmaceutical company, one of the producers of the COVID-19 vaccine, to turn this innovation into a world-changing solution.
“Engineering biology offers immense potential to disrupt our fossil fuel dependency, build a circular economy, and create sustainable chemicals and materials,” the team stated. “We welcome potential collaborators to get in touch.”