The new 36 kV connection standard, introduced to optimize renewable energy integration into the transmission grid, can now rely on Prysmian’s most advanced cable and monitoring system solutions. These are cutting-edge products designed to deliver high performance with minimal environmental impact.
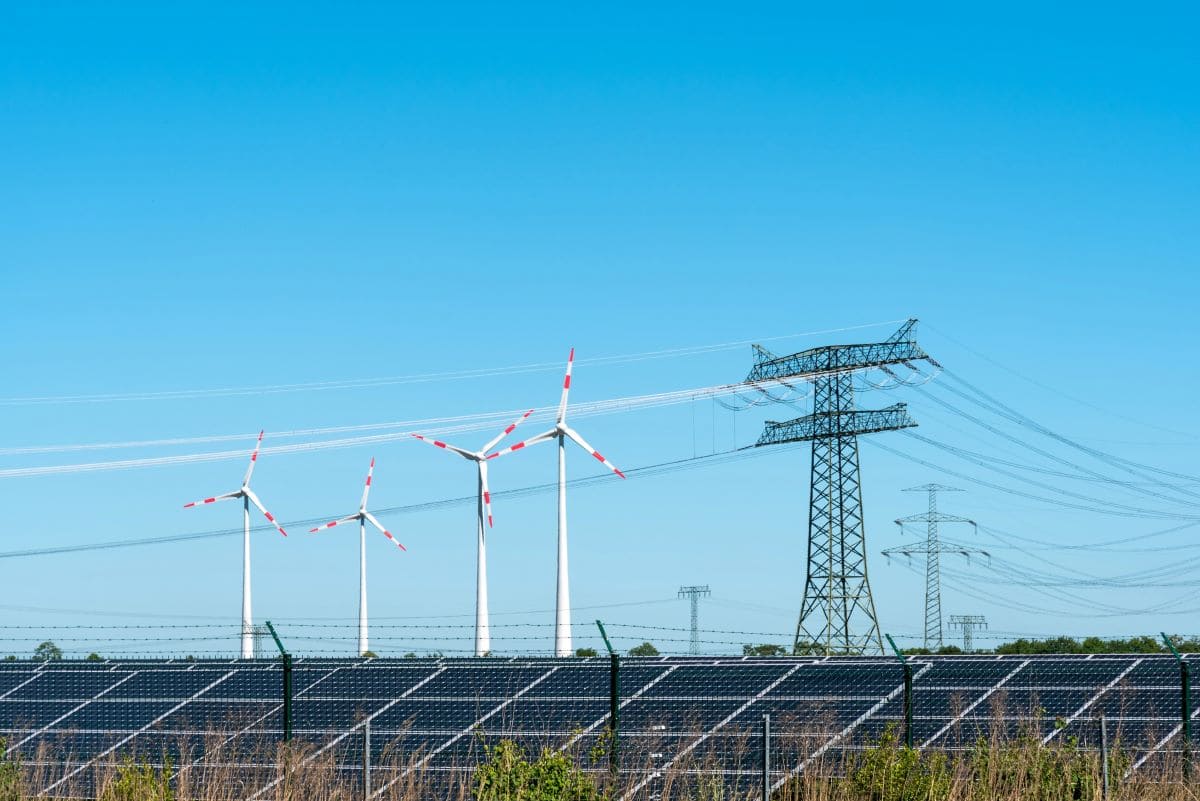
Prysmian, enabler of the energy transition
A major upgrade is reshaping the national power grid: the 36 kV connection standard, introduced by Terna to streamline the integration of renewable energy sources while simplifying connection procedures and reducing environmental impact.
The new standard has been welcomed by the industry but has also introduced new technical demands—especially for cable systems. Prysmian, the global leader in energy and telecom cable solutions, responded swiftly, as demonstrated at the KEY 2025 expo.
At the Rimini event, Prysmian showcased its latest innovations supporting the energy transition, including a complete portfolio designed for the 36 kV standard: P-Laser cables rated 20.8/36 kV, system accessories, and advanced monitoring tools. All backed by highly trained teams of installers and testers.
A grid in transformation: connection challenges
The rapid expansion of renewable energy installations is challenging not only system flexibility but also grid integration. According to Terna, as of February 28, 2025, over 6,000 requests for connection to the national transmission grid (RTN) had been submitted, totaling more than 354 GW in capacity. Most projects are under 10 MW, with an average size of around 35 MW in 2023.
This is where the issue begins. Traditional RTN connection schemes use 150–132 kV bays within 380/150 kV substations—sized for projects of 200–250 MW, far above the average capacity of most renewable installations.
This mismatch leads to inefficiencies. Each project is typically assigned a dedicated bay, resulting in poor land use and added technical and bureaucratic hurdles. Developers must manage voltage step-up themselves, which increases project complexity and cost.
The 36 kV connection standard
To improve infrastructure efficiency, the idea of shared 150 kV bays—so-called “condominium” connections—has gained ground. This approach reduces the need to build new lines and limits environmental impact, but it adds complications in permitting and construction phases, slowing connection timelines.
This is where the new 36 kV standard comes in.
Under the new model, each renewable plant connects directly to a 36 kV bay that acts as a grid facility for projects up to 100 MW. This allows connections at a more suitable voltage level while removing the permitting burdens associated with 150–132 kV infrastructure. With this setup, Terna—not the developer—handles voltage step-up beyond 36 kV.
From proposal to approval
“ ,” stated Terna when launching a consultation in August 2021 on the revised Annex A.2 of its Grid Code.
The update was submitted to ARERA on October 15, 2021. Just days later, the regulator approved it (resolution 439/2021/R/eel), and Terna published the updated version on October 20, 2021. In May 2022, further updates to Sections 1C, Annex A.17, and Annex A.68 of the Grid Code aligned them with the new Annex A.2, establishing technical requirements for producers.
By December of that same year, more than 1,400 36 kV connection offers had been issued, covering over 56 GW of renewable and storage capacity. Notably, over 40% of the offers are revised requests at 36 kV for projects that had previously received connection proposals at 220–150–132 kV.
Why the 36 kV standard matters
The new standard enables more efficient use of transmission infrastructure by avoiding oversized bays and reducing land use. It also simplifies the developer’s job by shifting voltage step-up duties to the grid operator.
As Terna highlights, 36 kV connections allow multiple developers to share a single 380–220–150–132/36 kV transformer, eliminating the need for individual 150/36 kV transformers. This reduces land use, improves local acceptance, and accelerates permitting by minimizing visual and environmental impact.
Additionally, it reduces overall system costs by allowing more rational expansion of the transmission network.
Prysmian’s 36 kV-ready cable solutions
Despite the benefits, developers quickly faced a challenge: sourcing cables that meet the new technical requirements—especially in terms of insulation and nominal voltage. Using undersized cables risks system failure and shortens asset lifespan.
That’s where Prysmian comes in. The company, known for sustainable innovation and technological leadership, has developed cable solutions tailored to the new 36 kV standard.
With more than 130 years of experience and ongoing investment in research and development, Prysmian holds a leading position in the design, manufacturing, and installation of cable systems for renewable energy transmission. Its product range delivers superior electrical performance, reduced costs, and a strong focus on environmental impact.
That same commitment drives Prysmian’s new line of solutions developed specifically for the 36 kV connection standard.
20.8/36 kV P-Laser cables by Prysmian
Prysmian’s lineup includes two 20.8/36 kV cables (Um 42 kV) using P-Laser technology—the first fully recyclable, high-performance cable system based on High Performance Thermoplastic Elastomer (HPTE), a proprietary material. P-Laser technology ensures enhanced electrical properties, including high intrinsic reliability and improved performance at elevated temperatures.
While well known in the renewables sector, this technology now powers two new solutions: the P-Laser ARP1H5E cable and the P-Laser ARP1H5 (AR) E cable with AIRBAG technology. Both are rated at 20.8/36 kV, single-core, compact, and fully compatible with traditional cables and accessories. They deliver outstanding performance and can operate at higher temperatures—up to 130°C—an essential feature under overload conditions.
One of the key strengths of these solutions, in addition to a low-emission manufacturing process, is their full recyclability. Each kilometer of P-Laser cable enables recovery of 500 kg of high-quality recyclable plastic—helping the energy sector move closer to circularity.
The AIRBAG version adds a protective layer beneath the outer sheath to absorb mechanical shocks and prevent permanent deformation. This feature is ideal for direct burial and allows shallower installation without additional protective layers, reducing costs by eliminating the need for sand bedding.
Accessories and monitoring systems
Prysmian’s offering includes a full range of accessories for 36 kV systems, such as Elaspeed joints that integrate all necessary insulation and protection functions. Made with cold-shrink EPDM technology, they require no special tools and are suitable for many applications. The Elaspeed S version includes sensors to detect voltage or partial discharges during maintenance.
The product line also includes integrated monitoring systems for predictive maintenance in high-demand scenarios. These tools measure partial discharges, shield currents, distributed temperature, and load levels, and are paired with remote diagnostics that notify operators of system alarms in real time.
In collaboration with Prysmian