The most expensive materials in sustainable automotive, like recycled carbon fiber and aluminum, are reshaping the future of low-impact mobility.
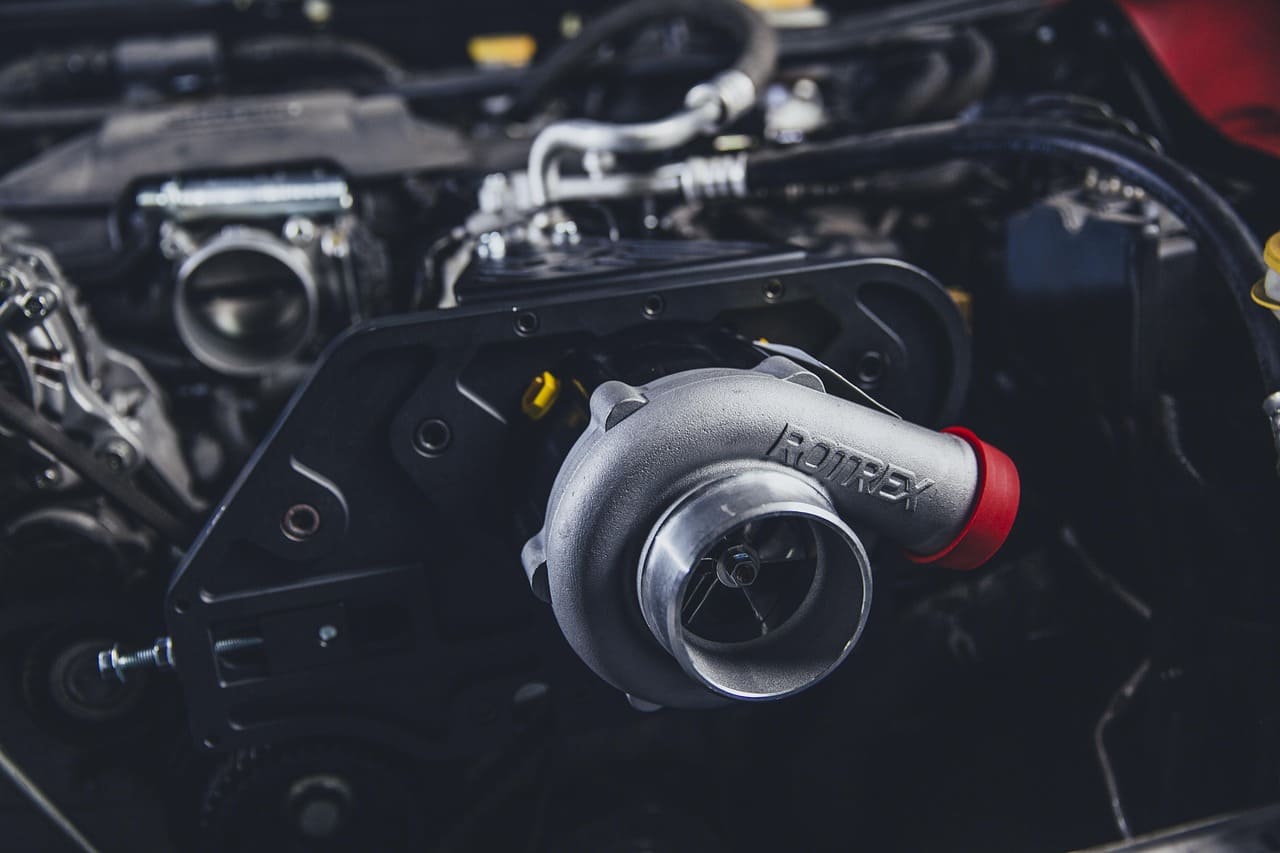
In recent years, the concept of sustainability has taken firm root in the automotive sector, pushing manufacturers to rethink their entire production processes. While the focus was once limited to engine efficiency and tailpipe emissions, today the full vehicle lifecycle is under scrutiny. A complex and fascinating challenge is integrating recycled materials without compromising quality, performance, or safety.
But not everything recycled is inexpensive. Some materials, even when recovered, remain among the most expensive to handle and reuse. Understanding which ones and why they retain such high value reveals the true cost of sustainability in the auto industry. This includes not only raw materials but also components such as used trailer hitches, now easier to source thanks to online platforms offering original and refurbished parts.
Recycled carbon fiber: the luxury of lightweight sustainability
Among the most prized materials, recycled carbon fiber holds a place of distinction. Long used in motorsports and premium models for its unmatched strength-to-weight ratio, it has always been both an engineer’s dream and an accountant’s nightmare. Traditional production is energy-intensive and technologically demanding, driving up costs.
Recycling carbon fiber is far from straightforward. Extracting usable fibers from composites without degrading mechanical properties requires advanced techniques like pyrolysis or solvolysis. Even then, the resulting fibers are often shorter and less performant, requiring further processing before reuse.
Still, demand for recycled carbon fiber is rising—especially for parts like interior panels, spoilers, and secondary structural components. In the push for lighter electric vehicles that maximize efficiency, the material is a strategic investment. Its high cost reflects not just recycling complexity but also its enduring functional value in sustainable automotive design.
Recycled aluminum: energy savings come at a price
Aluminum is another major player in sustainable automotive transformation. Celebrated for its light weight and ability to boost energy efficiency, it’s particularly favored in EVs and luxury models. Yet using recycled aluminum presents challenges that influence its final cost.
Purity is the biggest hurdle. Recycled aluminum must meet strict quality standards, especially for structural parts. Even minor contamination can compromise safety, requiring costly sorting, melting, and remelting procedures.
Brands like Jaguar and Land Rover are heavily investing in “closed-loop manufacturing” systems to internally recover and reuse aluminum. The energy advantage is substantial—recycling requires just 5% of the energy needed to produce aluminum from bauxite. However, the technology investment needed to achieve this level of quality keeps prices high. It’s a clear example of how energy savings still demand financial commitment, particularly during the early stages of industrial transformation.
Recycled thermoplastic elastomers: innovation with a price tag
Less known to the public but vital to the industry, thermoplastic elastomers (TPEs) combine the flexibility of rubber with the processability of plastic. They’re found in everything from floor mats to seals and interior trim.
Recent advances have led to TPE compounds made with up to 73% recycled content—an impressive achievement in polymer chemistry. But integrating recycled input without compromising mechanical strength, thermal resistance, or dimensional stability is a high-stakes challenge requiring significant R&D and specialized manufacturing.
It’s not enough to simply mix virgin and recycled material. Formulations must be carefully engineered to meet the demanding specs of OEMs (Original Equipment Manufacturers). As a result, recycled TPEs remain relatively expensive compared to more conventional recycled plastics, despite their meaningful contribution to sustainability.
Other materials: lower costs, strategic value
Alongside premium materials, more affordable options like recycled steel and plastics play a vital role in advancing automotive sustainability.
Recycled steel, for instance, can cut emissions dramatically versus mining virgin ore. Energy savings from steel recycling are estimated at 60–70%, making it a critical material for greener vehicle production. High-strength lightweight steel also helps reduce vehicle weight without compromising safety—a key benefit as we transition to electric mobility.
Likewise, recycled plastics are increasingly used in non-structural parts such as interior trims or technical housings. Though less advanced than recycled carbon fiber or TPEs, they help improve the overall environmental footprint of next-generation vehicles.
Conclusion: sustainability is an investment worth making
Recycling in the automotive sector is not just about cost-saving—it’s a statement of purpose. Incorporating high-quality recycled materials is both a technical challenge and a long-term commitment to a more sustainable future.
Carbon fiber, aluminum, and polymer compounds prove that innovation, though expensive, is essential to cutting the environmental impact of mobility. In a market increasingly shaped by climate concerns, investing in these materials enhances brand credibility and opens new avenues for innovation and differentiation.
The economic hurdles are real—but the direction is set. Tomorrow’s vehicles will be lighter, more efficient, and more responsible, built in part from what once was waste.