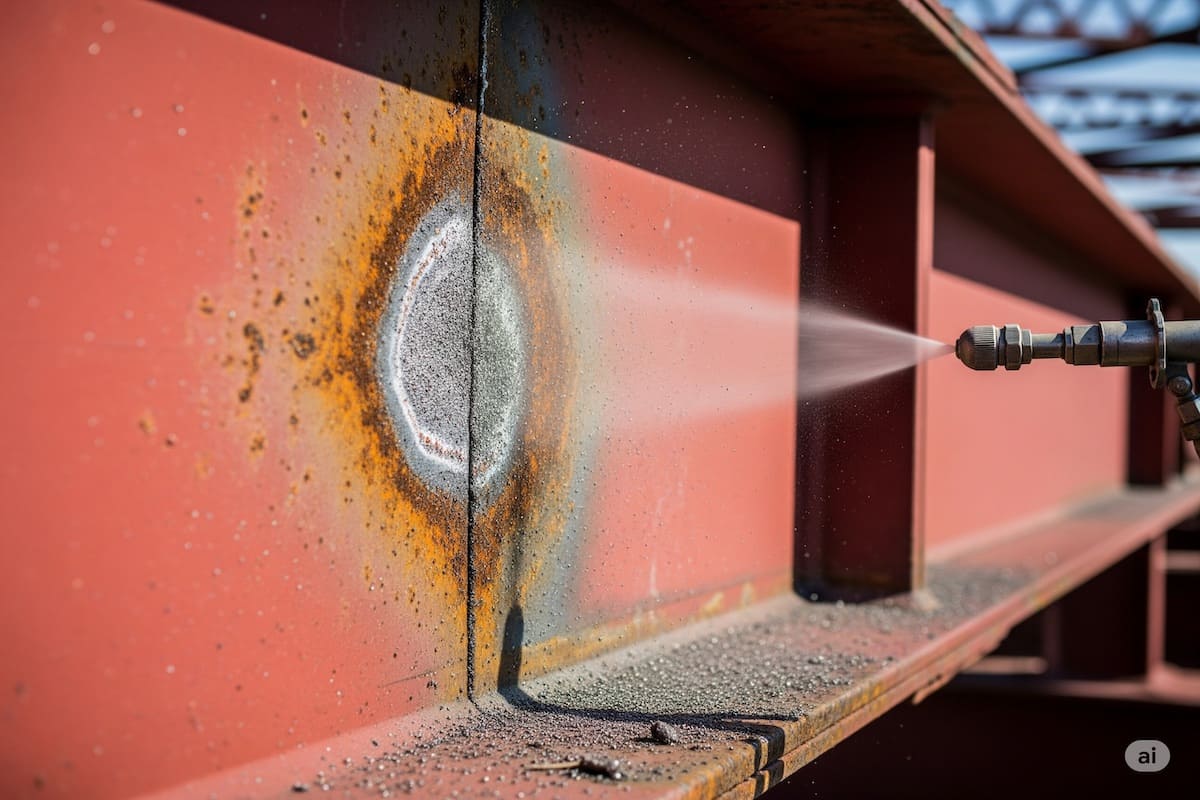
Bridge collapse, corrosion, and the urgent need for innovation
Nearly seven years ago, the city of Genoa was shaken by the tragic collapse of the Morandi Bridge, an event that killed 43 people, injured hundreds more, and displaced over 560 residents. Sadly, this was just one of many bridge disasters, often caused by aging, corrosion, and poor maintenance.
Now, a team from the University of Massachusetts Amherst has developed an innovative “cold spray” system that uses 3D printing technology to repair structural damage in bridges and key infrastructure. The approach is minimally invasive and cost-effective.
Nearly half of US bridges need repair
The project is a collaboration between UMass Amherst and researchers from the Department of Mechanical Engineering at MIT. The goal is to test the new technology on a pilot bridge and eventually scale the solution across the country.
The urgency to prevent bridge collapse and improve road infrastructure is clear. According to the American Society of Civil Engineers’ Report Card for America’s Infrastructure 2025, 49.1% of the 623,218 bridges in the US are in “fair” condition and 6.8% are in “poor” condition. The estimated cost to restore them exceeds $191 billion.
How cold spray works in bridge maintenance
Last month, the research team conducted a proof-of-concept repair on a corroded section of a bridge in Great Barrington, Massachusetts. The cold spray technique reinforces steel beams by layering metal powder at high speed, restoring strength and extending lifespan.
This additive method, similar to 3D printing, builds up layers of steel over damaged areas, increasing their structural integrity with each application.
Cold spray has already proven effective in repairing large-scale assets like submarines, aircraft, and ships. Bridges, however, pose unique challenges. Unlike mobile vehicles, bridges cannot be brought into a repair facility. The 3D printer must go to the structure, not the other way around.
Moreover, these interventions must be done without causing major traffic disruptions, a key benefit of this mobile and flexible repair method.
Digital tools accelerate the repair process
Part of the innovation lies in replacing traditional visual inspections with 3D LiDAR scanning. This allows researchers to precisely detect corrosion, develop an accurate digital repair plan, and deposit material only where it’s needed.
The pilot bridge used in this study is scheduled for demolition in a few years. Before that happens, the beams treated with the spray method will be transported to MIT for full analysis and testing. This will allow the team to assess the strengths and limitations of cold spray repair, monitor any post-treatment corrosion, and test the mechanical resistance of the reinforced sections.
The research findings are available at the following [link].