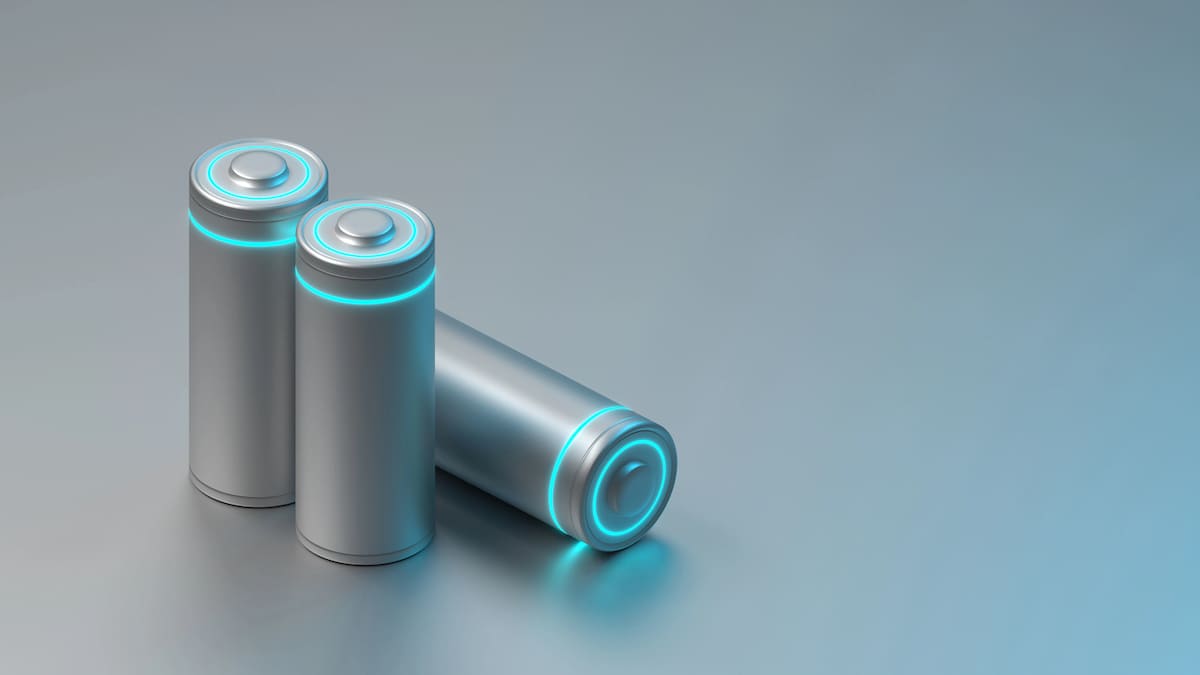
Fast-charging lithium-sulfur batteries, challenges and strategies
A new international review highlights how lithium-sulfur batteries could overcome current limitations
The new frontier of ultra-fast recharging
Rechargeable lithium-sulfur batteries that charge in under 15 minutes without losing capacity are no longer a dream. But achieving this goal requires precise direction in today’s research. That’s the key message from a new international study offering a roadmap for practical, safe deployment of this promising technology.
Conducted by researchers at Kiel University, Shiv Nadar Institution of Eminence, and Yuan Christian University, the study reviews the most recent literature on the topic. It identifies the mechanisms that allow these batteries to operate stably and efficiently even under high-speed charging conditions.
This in-depth analysis sheds light on future development paths for a new generation of rechargeable batteries with major implications for electric vehicles and portable electronics.
What are lithium-sulfur batteries and how do they work?
Lithium-sulfur (Li-S) batteries are rechargeable batteries known for their high specific energy (gravimetric energy density). A typical cell consists of:
- a sulfur cathode
- a lithium metal anode
- an organic electrolyte
- a separator
During discharge, the lithium anode oxidizes, releasing electrons and Li+ ions. The electrons flow through the external circuit while the lithium ions travel across the cell and intercalate reversibly into the cathode structure – a process known as lithiation. This triggers a multi-step reaction that reduces sulfur to lithium sulfide (Li₂S).
Conversely, during charging (cathode delithiation), the Li₂S is oxidized to regenerate sulfur through several intermediate steps.
Advantages and drawbacks of lithium-sulfur batteries
Li-S batteries offer undeniable benefits, starting with a theoretical energy density of 2,600 Wh/kg—about 10 times higher than that of conventional lithium-ion batteries. Another advantage is sulfur itself: it is cheap, abundant, and non-toxic.
However, commercialization of lithium-sulfur batteries lags significantly behind that of lithium-ion technology, due to several technical hurdles. Today, key challenges limit coulombic efficiency and the stability of charge-discharge cycles.
These include the cathode’s volumetric expansion (up to +80%), material degradation, and the so-called shuttle effect – where intermediate polysulfides migrate between the cathode and anode during sulfur reduction. Additionally, sulfur is a natural electrical insulator and must be combined with conductive additives to improve performance, which adds extra weight.
A strategy to improve lithium-sulfur batteries
The new international review specifically focused on Li-S systems designed for fast charging (under 30 minutes) and with high sulfur loading. By analyzing around 100 studies, the researchers identified the challenges slowing down fast charging, their impact, and the corresponding strategies to overcome them.
“The ability of lithium-sulfur batteries to achieve fast charging is fundamentally governed by the kinetics of sulfur redox reactions, particularly the conversion between different polysulfide species and the final formation of solid Li₂S,” the authors wrote. “Material design plays a crucial role in accelerating these slow kinetics, especially under the high current densities required for fast charging.”
The study combines materials science, electrochemistry, nanotechnology, and engineering into an integrated approach. It introduces a new methodology that serves as a guide to developing lithium-sulfur batteries that are not only fast-charging, but also powerful, durable, and safe. The result is a practical roadmap for bringing fast-charging Li-S batteries to electric mobility and stationary energy storage applications.
Approach | Advancements | Challenges (hindering fast-charging) | Future directions |
---|---|---|---|
Cathode/electrode design | Optimized hierarchical/conductive structures enhance utilization, ion transport, stability. | Balancing high S loading/capacity with integrity, stability at high currents. | Scalable fabrication of advanced microstructures for enhanced ion transport and high S loading. |
Catalytic materials | Advanced catalysts improve SRR/SER kinetics and reduce shuttle effect. | Cost-effective synthesis, scalability, and long-term stability under operating conditions. | Designing efficient, durable, affordable catalysts for large-scale use. |
Separator modifications | Functional coatings/layers trap LiPS, regulate ion transport, reduce dendrites, improve stability. | Stable, cost-effective, scalable modifications without significant resistance increase. | Refining techniques/materials for multi-functionality (trapping, ion transport, anti-dendrite) and long cycle life. |
Electrolyte optimization | Diverse formulations (Ether+additives, HCEs, SSEs, etc.) explored for high-rate/lean conditions and stability. | Balancing high ionic conductivity with Li-metal stability and shuttle suppression. | Novel formulations (incl. additives, solid/hybrid) for improved safety, compatibility, operating window and cost. |
Anode stabilization | Strategies developed (artificial SEI, composites, coatings, 3D structures) for anode protection. | Preventing dendrites and maintaining high CE during sustained high-rate cycling. | Developing robust, scalable, cost-effective anode protection methods. |
Novel chemistries/pathways | Monoclinic γ-sulfur enables direct solid-state conversion (potentially avoids LiPS shuttle, allows high rates). | Integrating novel chemistries (like γ-S) with practical, high-loading, scalable designs. | Optimization and validation of direct conversion pathways and compatible architectures. |
AI/ML applications | Accelerating materials discovery, optimizing charging protocols, performance prediction/analysis. | Effective R&D integration, data handling, model accuracy/reliability. | Wider adoption for streamlined development, adaptive BMS, improved lifetime management. |
Scalability and manufacturing | Exploration of potentially scalable processes. | Cost-effective, high-volume manufacturing of advanced components; Quality control and reproducibility. | Developing cost-effective materials synthesis and scalable, precise manufacturing for commercialization. |
Credit: Advanced Energy Materials (2025). DOI: 10.1002/aenm.202404383
The full study is published in Advanced Energy Materials.